Revolutionizing Zinc Production with Cutting-Edge Automation and Robotics
Boliden Kokkola is a world-class zinc producer, recognized for its top-tier utilization of the latest technology. The latest major technology investment is the foundry’s fully automated third casting line. With two other casting lines already automated, all lines in the foundry can now be monitored from the control room.
At the foundry, new technology is utilized in various ways. At the start of the casting process, automatic forklifts transport zinc cathodes to the melting furnaces, and robots handle slag removal and product marking. Laser technology and 2D codes are used for marking, enabling machine identification and matching of products to sales orders in the final production stage.
“With automation and robotics, we can significantly improve our operations and, above all, enhance work safety and ergonomics. The value of work increases when mechanical and heavy tasks are eliminated, allowing people to focus on tasks that require their skills,” says Vesa Törölä, GM of Boliden Kokkola.
Robots are also employed in electrolysis, where two automated anode cleaning stations operate.
“At these stations, robots maintain almost 40,000 anode plates every month. They move heavy anodes along the line and install and remove plastic insulators and conductors. Additionally, the condition of the anodes is checked using machine vision. The automated and robotized maintenance line has increased the value of work by transferring monotonous and burdensome tasks to robots,” says digitalization manager Marko Salmi.
Machines and robots can perform repetitive tasks more efficiently than humans. This allows people’s skills to be concentrated in more meaningful work units, changing the nature of the work. Expectations for higher skill levels among employees have grown and will continue to grow. As work evolves, employees can focus on process control, equipment maintenance, and development tasks, which offer challenges and require new skills. The goal is to create a pleasant work environment for everyone.
“Employees have a wide range of tasks requiring special expertise in automation, digitalization, and IT. The modern zinc plant is a vantage point for utilizing the latest technology,” continues Törölä.
Fundamental for the plant
“Long-term automation and digitization are fundamental for keeping the zinc plant and its operations in Finland. There is a need for efficient and responsible zinc production in Europe,” says Törölä.
Boliden Kokkola is one of the largest zinc plants in the world. It has long been at the forefront of technology utilization and will continue to innovate. Digitization and automation are central to the strategy of the plant as the entire organization.
“In the future, we will invest in proactive systems that optimize process control and system maintenance. Video analytics, for instance, offer significant opportunities for monitoring product quality and industrial area safety,” says Salmi.
Virtual reality has also reached the industrial area with a simulation model of a semi-gantry crane. This virtual model provides a safe learning environment for employee training, allowing continuous work at the electrolysis around the clock.
Text: Marjukka Puolakka. Published in Keskipohjanmaa and Kokkola-lehti 10/2024.
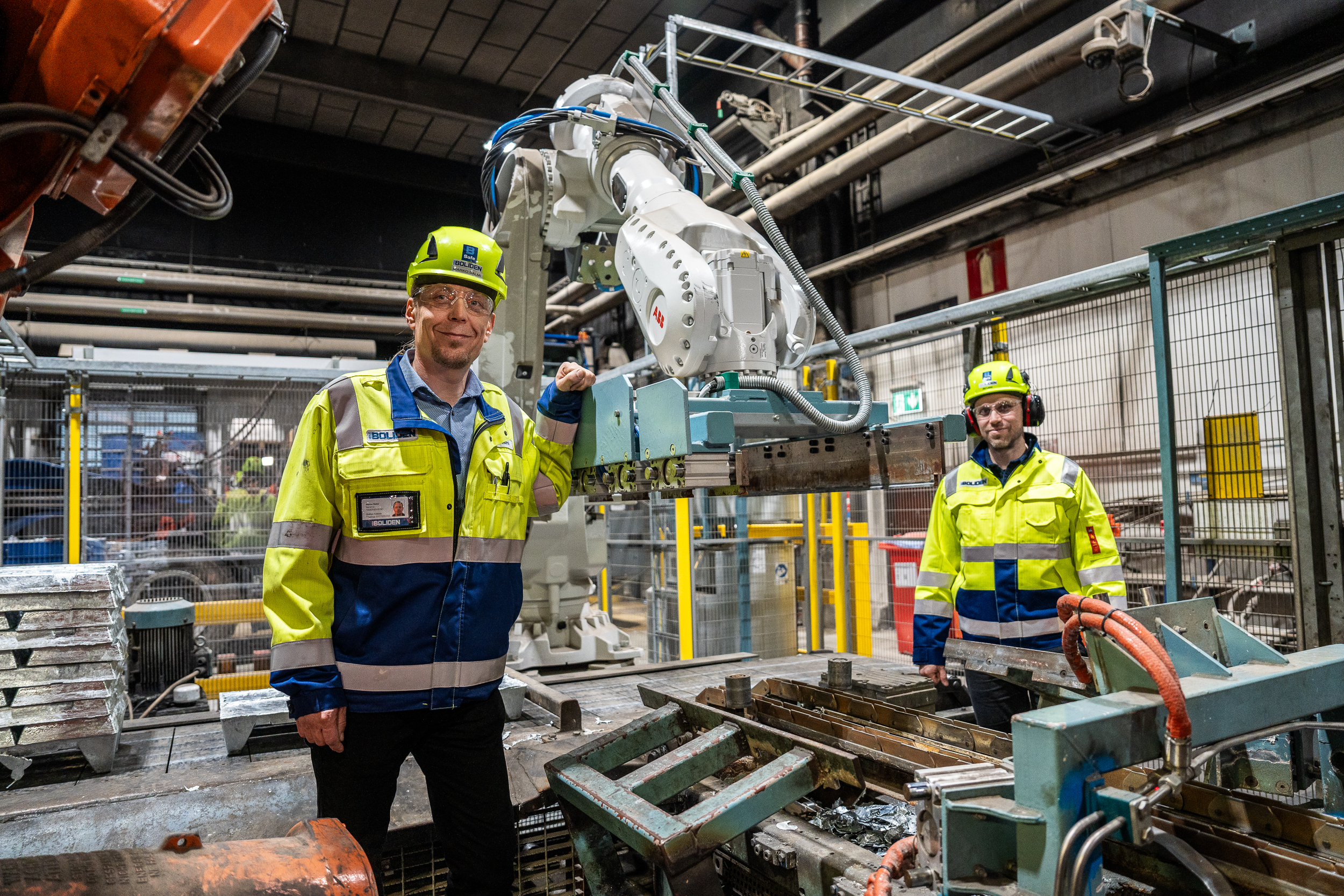